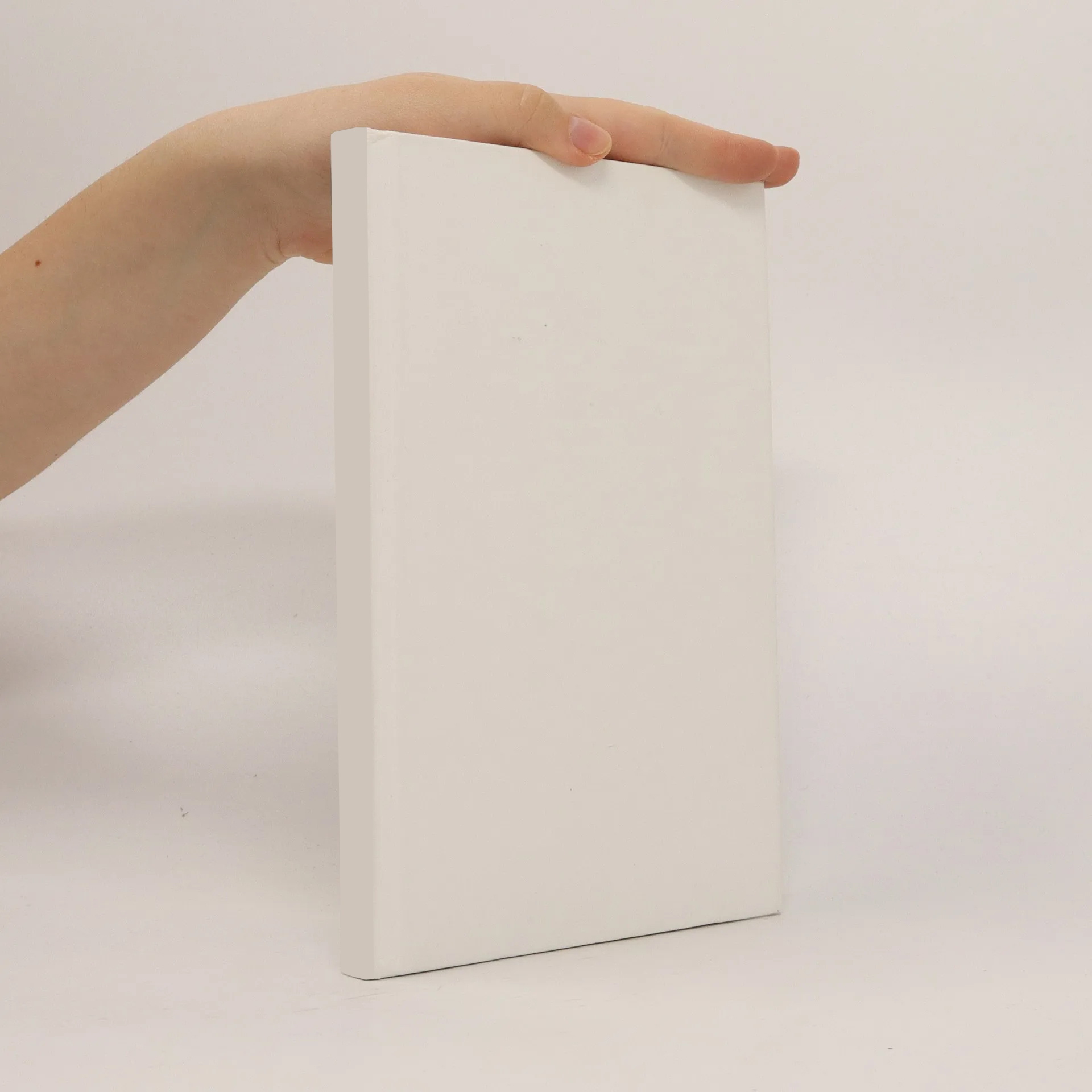
Parameter
Mehr zum Buch
In this dissertation, a high thermal gradient process, the downward directional solidification process (DWDS), has been extensively studied in the application for casting single crystal Ni-based superalloy components. It can be achieved that the DWDS process has a capability to significantly enhance the thermal gradient and reduce the differences in this value along the height of the component as well as two different sizes of castings during the directional solidification of single crystal superalloy components. The enhanced thermal gradient and shorted interval in this value not only allow much faster solidification rates, but also result in a substantial refinement of the cast microstructures, an improvement of the segregation degree of alloying elements, a reduction in the size and volume fraction of microporosity, an increase of the microstructural homogeneity. The DWDS process can eliminate the freckle-type defect in essence by investigating the segregation and density profiles in the mushy zone. Gradually refined microstructures and reduced segregation of the alloying elements are observed in the DWDS solidified samples with increasing the withdrawal rates. The evolution of the primary dendrite arm spacings with the withdrawal rates can be reasonably described by the theoretical model of Bouchard and Kirkaldy which considers the convection factor, when the dendrite-calibrating factor is assumed to be 13.5. Additionally, the solidification sequence of the eutectic pool commences with a fine (γ+γ′) structure in the center of interdendritic regions or adjacent to γ phases, then progresses spatially and develops a petal-like coarse (γ+γ′) structure. Following this sequence, γ′ particles precipitate from the γ phase between the impinging coarse petal-like γ′ phases.
Buchkauf
Microstructural investigation of downward directionally solidified single crystal superalloys, Fu Wang
- Sprache
- Erscheinungsdatum
- 2015
Lieferung
Zahlungsmethoden
Keiner hat bisher bewertet.