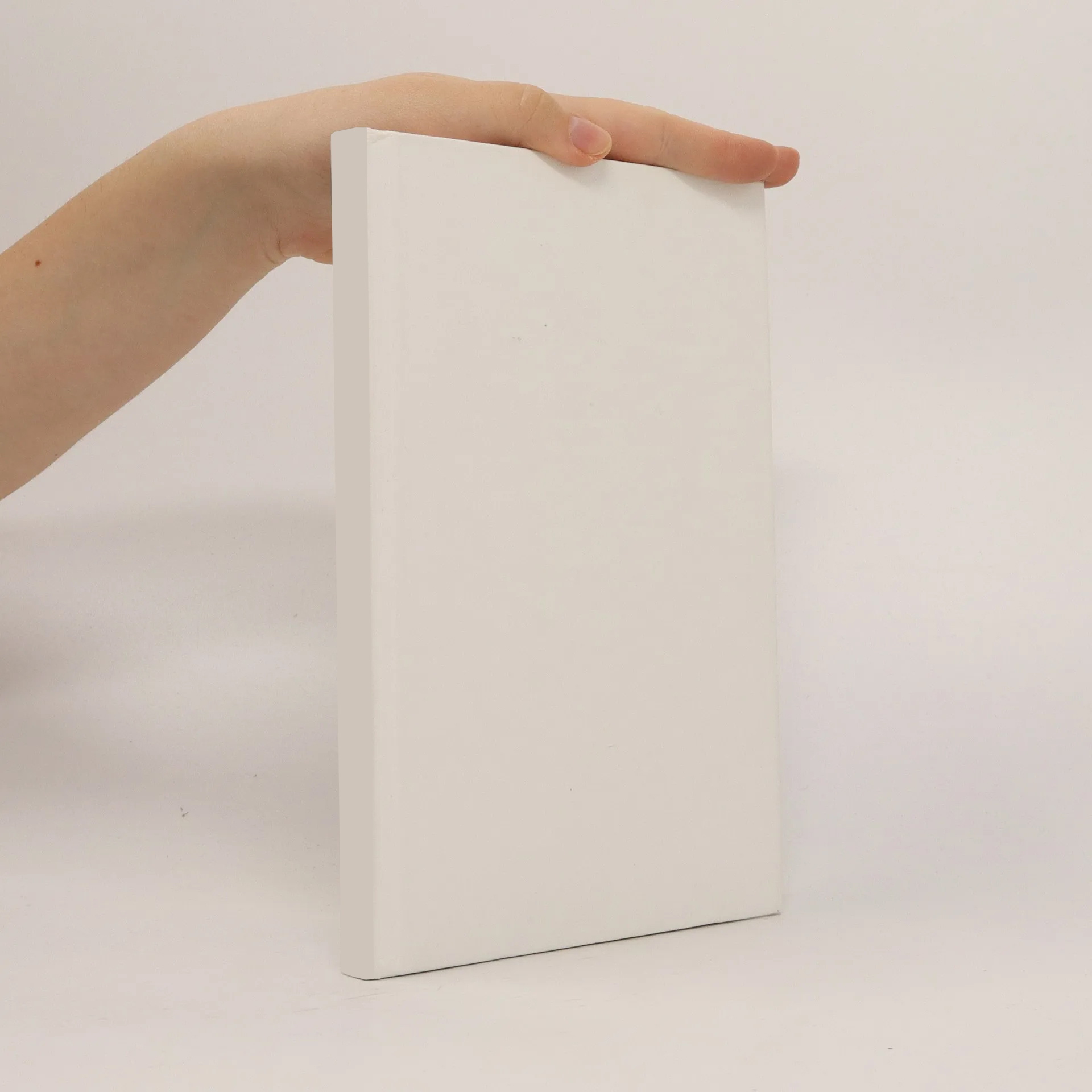
Parameter
Kategorien
Mehr zum Buch
Finite element simulation has become an important tool in understanding the chip formation process. Complex machining processes with complex chip morphologies have been simulated this way. An important challenge in the modelling of machining processes is that material parameters are not available which can robustly predict the material behaviour at large ranges of strains, strain rates and temperatures. During a continuous chip formation process, strains can reach up to 200%, strain rates can be of the order of 105 s−1 and temperature variation can be in the order of hundreds of degrees. In comparison, state-of-the-art experimental methods such as the Split Hopkinson Pressure Bar (SHPB) tests can usually reach strains of up to 50% and strain rates of the order of 103 s−1. Data fitting techniques are then used to identify material parameters from the experimental data. Due to the large extrapolations involved, the machining simulation results do not robustly match the experimental results. The difficulty of using the material parameters determined from standard experiments for machining simulations is first shown for three different materials. The Johnson-Cook material parameters are obtained for Ti-15-3-3-3, Ti-6246 and Alloy 625 from SHPB experiments. These are then used to simulate the chip formation using the finite element method. For Ti-15-3-3-3 and Ti-6246, segmented chip formation is observed. For Alloy 625, the Johnson-Cook model overestimates the material strength at high strains and the resulting machining simulation gives rise to a continuous chip. Therefore a modified Johnson-Cook model is used for machining simulations which forms segmented chip. The average cutting force in the three cases are predicted within 20% of the experimentally obtained values. There are significant differences in the predicted chip shapes and the experimentally obtained chip shapes. These differences can be attributed to the difficulty of predicting the material behaviour at conditions prevailing during machining. An inverse identification method is used to identify material parameters directly from machining processes to resolve this problem. The chip shapes and the cutting forces are matched to a standard by systematically varying the material parameters. The robustness of the method is tested by identifying parameters for two different materials and conducting optimisations from different starting points. Studies are also conducted to improve the convergence and reduce the computational expense. The knowledge of the effect of stress-strain curves on the chip shapes and the cutting forces can also be used to improve the optimised solution predicted by the inverse identification algorithm. This can lead to reduction in the computational expense. It is observed during the identification process that a number of parameter sets can be found which give rise to similar chips and cutting forces. This is because all the different parameter sets represent the same flow stress curve in the domain of machining. In order that the identified parameters are valid over a large machining domain, widely varying cutting conditions are chosen for the identification process.
Buchkauf
Inverse identification of material parameters from machining processes, Aviral Shrot
- Sprache
- Erscheinungsdatum
- 2013
Lieferung
Zahlungsmethoden
Feedback senden
- Titel
- Inverse identification of material parameters from machining processes
- Sprache
- Englisch
- Autor*innen
- Aviral Shrot
- Verlag
- Cuvillier
- Erscheinungsdatum
- 2013
- ISBN10
- 3954043971
- ISBN13
- 9783954043972
- Kategorie
- Skripten & Universitätslehrbücher
- Beschreibung
- Finite element simulation has become an important tool in understanding the chip formation process. Complex machining processes with complex chip morphologies have been simulated this way. An important challenge in the modelling of machining processes is that material parameters are not available which can robustly predict the material behaviour at large ranges of strains, strain rates and temperatures. During a continuous chip formation process, strains can reach up to 200%, strain rates can be of the order of 105 s−1 and temperature variation can be in the order of hundreds of degrees. In comparison, state-of-the-art experimental methods such as the Split Hopkinson Pressure Bar (SHPB) tests can usually reach strains of up to 50% and strain rates of the order of 103 s−1. Data fitting techniques are then used to identify material parameters from the experimental data. Due to the large extrapolations involved, the machining simulation results do not robustly match the experimental results. The difficulty of using the material parameters determined from standard experiments for machining simulations is first shown for three different materials. The Johnson-Cook material parameters are obtained for Ti-15-3-3-3, Ti-6246 and Alloy 625 from SHPB experiments. These are then used to simulate the chip formation using the finite element method. For Ti-15-3-3-3 and Ti-6246, segmented chip formation is observed. For Alloy 625, the Johnson-Cook model overestimates the material strength at high strains and the resulting machining simulation gives rise to a continuous chip. Therefore a modified Johnson-Cook model is used for machining simulations which forms segmented chip. The average cutting force in the three cases are predicted within 20% of the experimentally obtained values. There are significant differences in the predicted chip shapes and the experimentally obtained chip shapes. These differences can be attributed to the difficulty of predicting the material behaviour at conditions prevailing during machining. An inverse identification method is used to identify material parameters directly from machining processes to resolve this problem. The chip shapes and the cutting forces are matched to a standard by systematically varying the material parameters. The robustness of the method is tested by identifying parameters for two different materials and conducting optimisations from different starting points. Studies are also conducted to improve the convergence and reduce the computational expense. The knowledge of the effect of stress-strain curves on the chip shapes and the cutting forces can also be used to improve the optimised solution predicted by the inverse identification algorithm. This can lead to reduction in the computational expense. It is observed during the identification process that a number of parameter sets can be found which give rise to similar chips and cutting forces. This is because all the different parameter sets represent the same flow stress curve in the domain of machining. In order that the identified parameters are valid over a large machining domain, widely varying cutting conditions are chosen for the identification process.