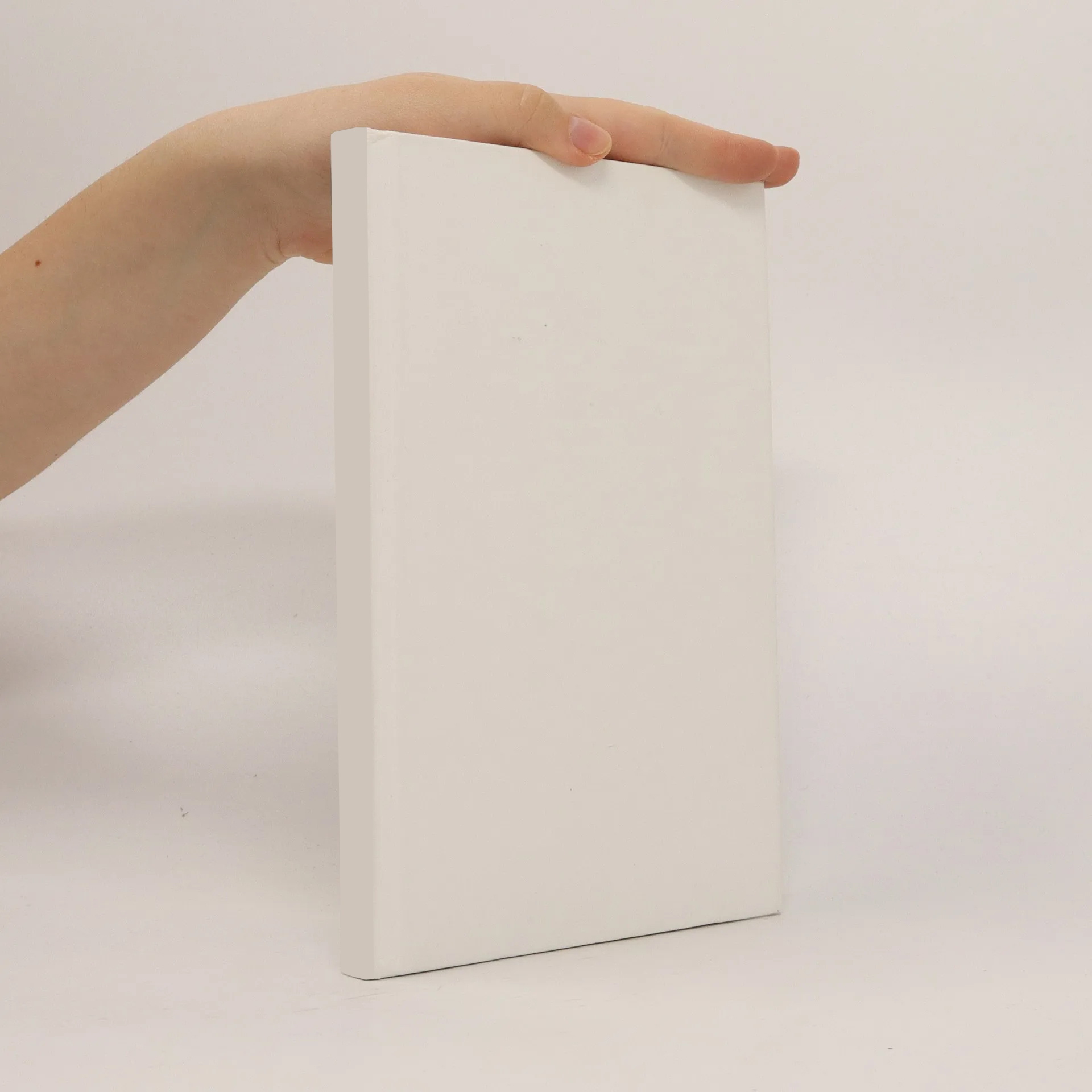
Mehr zum Buch
In the last decades, in response to the growing concerns over the environmental impacts of fluid power systems and their costs, manufacturers have been forced to develop more energy-efficient hydraulic components and decrease the used fluid volume by reducing the reservoir size. This leads to an increase of the installation space demand, which is often compensated by downsizing the tank. In contrast to this tendency, the hydraulic reservoir performs the function of releasing the accumulated entrained air to the surroundings. An underestimated tank size leads to a reduced air release capability, increasing the amount of free air drawn into the hydraulic system. This may cause problems, such as component damage, fluid degradation, noise production and poor system efficiency. The following work is a comprehensive study of the air release phenomenon in hydraulic reservoirs from the experimental and simulative point of views. To begin with, the air bubble behaviour in hydraulic fluids was measured in terms of bubble drag and coalescence. Using these results, a simulation code was implemented to predict the air release efficiency in tank geometries. Alongside this implementation, the air release in a test reservoir was measured. Finally, the code was validated with the in-house experimental results, exhibiting a good agreement. Thinking in terms of a tank as a lost design space can be very misleading. The main idea behind this dissertation is to treat reservoirs as a relevant component for the hydraulic system. The benefits of using cutting edge simulation and experimental tools to optimise the tank design are shown. They help save installation space and increase the system's efficiency through an air free hydraulic fluid.
Buchkauf
On the air release in hydraulic reservoirs, Marco Longhitano
- Sprache
- Erscheinungsdatum
- 2019
Lieferung
Zahlungsmethoden
Keiner hat bisher bewertet.